In-Depth Understanding of Dental Diamond Burs by Top Manufacturers
Dental diamond burs, made by top dental bur manufacturers, are essential for precise tooth tissue removal in contemporary dentistry, such as enamel or bone. Notable manufacturers, such as Brasseler USA, produce specialized designs, including the Brasseler football bur, tailored for specific dental tasks. Made from diamond, the hardest known material, these burs promise exceptional durability and precision. The craftsmanship of leading manufacturers, including pear-shaped dental bur producers, guarantees efficiency in a myriad of dental procedures, underscoring the significance of selecting the right manufacturer.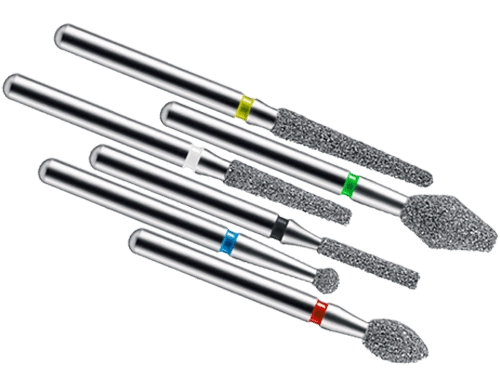
Expert Insights into Dental Bur Classifications by Leading Manufacturers
The classifications of dental burs, innovated by top manufacturers, are vital in dental care. This guide offers a detailed overview of these classifications:- Material Variants by Top Manufacturers: The transition from traditional steel to advanced materials like tungsten carbide and diamond is pivotal in dental technology advancements. Brasseler USA, for instance, excels in diamond burs, featuring a steel shank coated in natural or synthetic diamond powder. Synthetic diamond burs are prevalent for their cost-effectiveness, while natural diamond burs, offered by premium manufacturers, are valued for their superior quality and durability.
- Shank Types Across Brands: The shank type significantly impacts the bur’s functionality and speed. Leading producers offer a variety of shanks, including contra-angle, handpiece, and friction grip, each catering to specific operational needs.
- Diverse Shapes for Precise Procedures: Top manufacturers have tailored shape diversity, such as pear- and football-shaped burs (like the Brasseler football bur), for optimum performance in particular dental tasks, from cavity preparation to cosmetic detailing.
- Grit Size for Meticulous Work: The grit size determines the bur’s abrasiveness. Renowned manufacturers standardize grit sizes for simple identification, frequently by colored rings on the bur’s neck.
- Head Diameter for Versatile Applications: The head diameter, crucial for the size of the active portion of the bur, varies significantly, allowing dental professionals to select the ideal size for specific treatments, with top companies providing a comprehensive array.
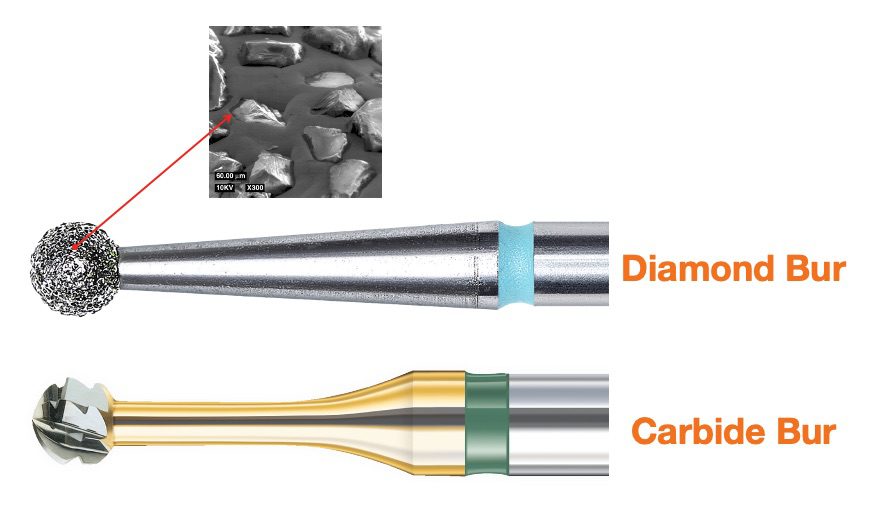
Comprehensive Analysis of Dental Diamond Bur Types and Applications
Examining the variety offered by leading dental diamond bur manufacturers reveals the extensive types and their specific uses:- Standard Diamond Burs for Routine Tasks: These burs, essential for grinding and shaping in dental procedures, are efficiently designed by reputable companies for routine dental work.
- Fine Diamond Burs for Detailed Finishing: Expert manufacturers design these burs for finishing and polishing, playing a critical role in achieving smooth surfaces and intricate contours in dental restorations.
- Coarse Diamond Burs for Robust Tissue Removal: Coarse diamond burs, developed by renowned manufacturers, are specifically engineered for cutting through hard dental tissues. Their coarse grit enables effective removal of tooth material.
Strategic Guide for Acquiring Dental Diamond Burs
Purchasing dental diamond burs involves various considerations:- Retail and Online Buying Options: The market offers multiple purchasing avenues, from traditional dental supply stores to online platforms. Online retailers are particularly noted for their convenience, competitive pricing, and extensive product range from leading dental bur manufacturers. Evaluating supplier reputation, customer reviews, and product assortment is crucial when selecting the best source for your dental needs.
Highlighting Notable Dental Diamond Bur Manufacturers
In the dental diamond bur sector, several manufacturers stand out for their exemplary products and services:- MDT Micro Diamond Technologies: Renowned for its FG Diamond & Carbide burs, MDT is known for innovation and quality, catering to clinical and laboratory applications.
- MEISINGER USA: With a legacy dating back to 1888, MEISINGER USA specializes in dental rotary instruments, including a diverse range of diamond burs.
- Strauss Diamond: Strauss Diamond’s commitment to quality and innovation in carbide & diamond dental burs makes them a preferred choice among dental practitioners.
- Brasseler USA: Known for its extensive product line, including the DuraBraze line, Brasseler USA is synonymous with quality and variety, catering to diverse dental needs.
- Veep Dental: As a leading supplier in China, Veep Dental offers a variety of dental equipment, adhering to international standards and enjoying a global reputation.
Crucial Considerations for Selecting a Dental Diamond Bur Manufacturer
Choosing the right manufacturer involves several key factors:- Quality and Certifications: Opt for manufacturers with ISO, FDA, and CE certifications, indicating a commitment to quality and safety.
- Product Range: A wide array of burs, in various types and sizes, is crucial for comprehensive dental care.
- Reputation: Manufacturers with a strong industry track record and positive customer feedback are preferable.
- Evidence of Efficacy: Case studies or real-life examples from manufacturers provide valuable insights into their products’ performance and applications.
- Innovation Commitment: Manufacturers investing in research and development demonstrate a progressive approach.
- Customer Support: Efficient customer service is vital for addressing inquiries and providing after-sales support.
Exploring the Future of Dental Diamond Burs
The dental diamond bur industry is evolving, marked by technological advancements and market growth:- Innovative Developments: Manufacturers are continually enhancing dental burs, improving their precision and functionality.
- Customization Trends: The rising demand for customized solutions has led manufacturers to offer personalized dental burs.
- Market Dynamics: The industry is experiencing robust growth, driven by specialized dental procedures and a focus on dental excellence.
- Regional Insights: North America leads in demand and innovation, highlighting the global scope of the dental burs market.
Conclusion
Selecting a dental diamond bur manufacturer is a critical decision in dentistry. This guide has provided a comprehensive overview of dental diamond burs, their types, classifications, and the criteria for choosing a manufacturer, along with insights into the industry’s future. This information aims to assist dental professionals in making informed choices, contributing to superior dental care and patient satisfaction.Dental diamond burs are specialized rotary tools used in dentistry for precise tooth tissue removal, shaping, and finishing procedures. Made from diamond particles, these burs are known for their durability and precision, making them ideal for tasks like cavity preparation, crown fitting, and cosmetic dental work.
Diamond dental burs are distinguished by their use of diamond particles, the hardest known material, which allows for superior precision and longevity. Compared to other types, such as tungsten carbide burs, diamond burs offer more efficient and precise cutting ability, making them suitable for intricate dental procedures.
Choosing the right dental diamond bur depends on several factors, including the specific dental procedure, the desired precision, and the material being worked on. Consider the bur’s grit size, shape, and type, as well as the manufacturer’s reputation and quality standards. It’s also important to match the bur to the dental handpiece you are using.
Yes, there are various quality grades for dental diamond burs, which are typically defined by the size and density of the diamond particles as well as the manufacturing process. Higher-quality burs usually feature finer, more densely packed diamonds, offering greater precision and a smoother finish. The choice between natural and synthetic diamond burs also affects the quality and price.
Dental diamond burs can be reused if they are properly maintained. It’s important to clean and sterilize them after each use to prevent cross-contamination and to maintain their cutting efficiency. However, their lifespan depends on their use frequency and the materials they are used on. Regular inspection for wear and tear is recommended to ensure optimal performance and safety.